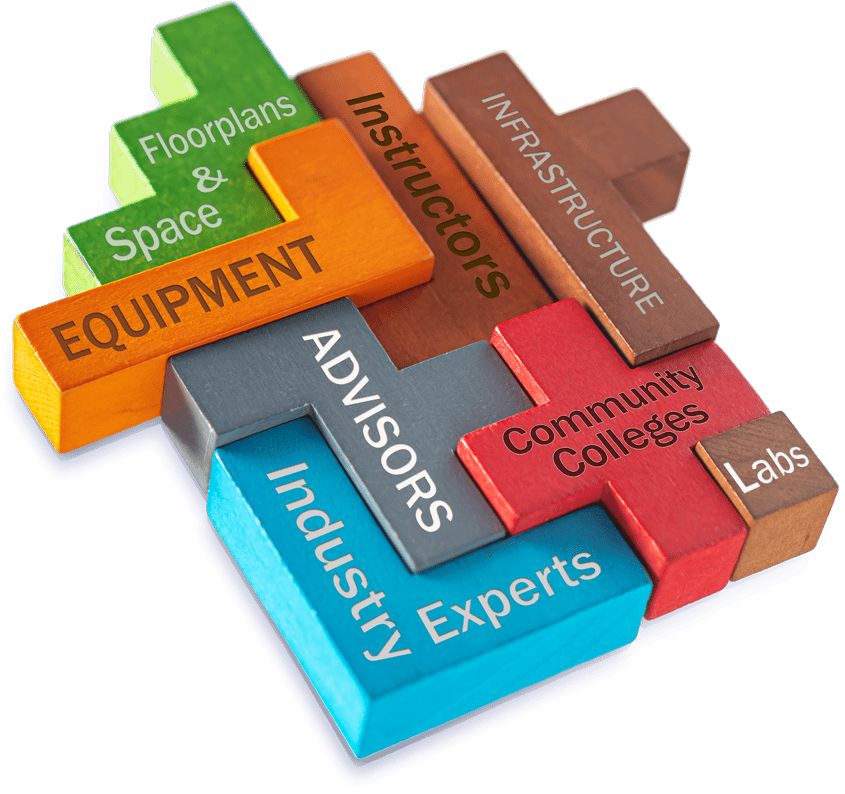
Think of it as a giant 3-D puzzle with complex pieces that often change, but somehow you have to make them all fit together. That is the task of AmeriCOM’s Technical Advisory Group whose members work with community colleges that are part of AmeriCOM’s optics ecosystems to establish and build optics training labs. So how do you go about putting the puzzle together? You start by assembling the right team.
Building a community college’s precision optics lab is an intricate, multi-faceted process that requires broad expertise.
“In order to work with each of the colleges around the country, we needed industry experts who have experience working with extremely sophisticated equipment,” explained Tom Battley, AmeriCOM’s Vice President of Government and Partnerships. “Our advisors not only have extensive industry experience, they also have great relationships with academia, and a technical understanding of the logistics necessary to build a lab.”
The group includes Mike Pomerantz who set up the 3,500 sq. ft. optics lab at Monroe Community College (MCC); Sterling Backus (based out of Colorado) and Paul Melone of Thorlabs; Navid Entezarian, also of Thorlabs, who helped teach students at Sussex County Community College (SCCC) in New Jersey before the school established its lab; and retired optics professional Paul Kelly. Ross Micali, whose expertise is in the area of apprenticeships and workplace skill development, is also part of the group.
Building an optics lab starts with the endgame in mind.
“Everything we build has to tie directly to the current needs of the optics manufacturing employers in a particular region.”
Mike Pomerantz
“That’s the point of everything we’re trying to build. From there we determine the skills and processes we want these students to learn.”
When a community college determines it wants to create an Optics Technology program, administrators first meet with employers to determine the relevant skills their curriculum should include. Then the lead instructor creates a list of equipment the lab should include to help train students in those skills.
The advisors meet regularly to review the equipment list and piece together how to construct the lab. “We have to look at everything,” Pomerantz said. “Does the facility have enough space for the equipment? Does it have the appropriate ventilation and power requirements? How do we configure the floorplan for all of the equipment with enough space for students to flow through? It’s a lot to figure out.”
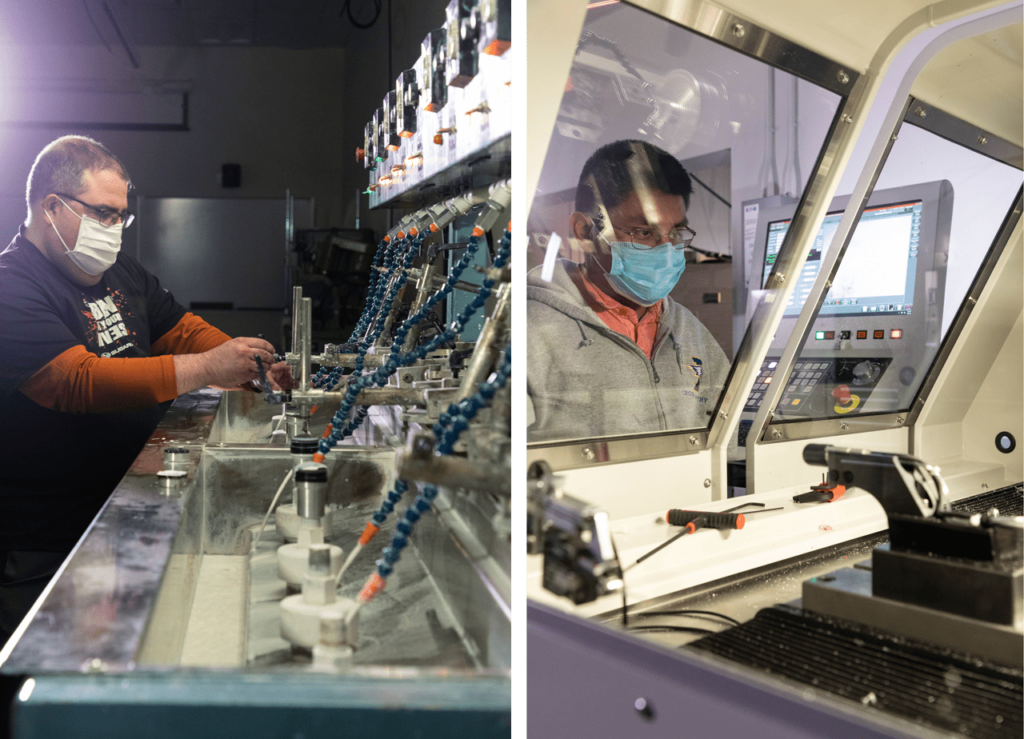
“It’s a complex problem to solve,” Battley said. “Even after we set up the labs there is ongoing troubleshooting and coordination with local employers, so we make sure the community colleges have open access to our group for support.”
AmeriCOM’s Technical Advisors have already helped establish optics labs at Front Range Community College in Colorado and SCCC, and work with additional colleges is underway. Group members say their work is just one piece of an even larger puzzle– that being the greater goal of strengthening the nation’s precision optics workforce.
“Our goal is to increase the capacity and quality of skilled optics technicians by a factor of 16 —from less than 50 per year to more than 800 per year by 2025,” Battley said. “That’s a big challenge, but together we can solve it.”